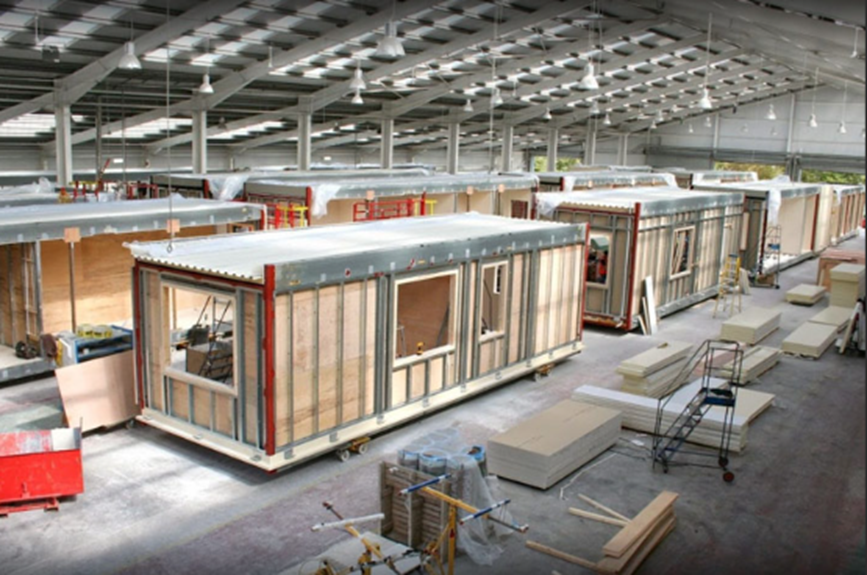
In recent years, the construction industry has witnessed a significant transformation driven by offsite construction methods. As the demand for faster, more efficient building solutions grows, real estate developers, modular factory owners, general contractors, and private equity firms are increasingly turning to prefabrication and modularity as viable alternatives to traditional construction. This blog post delves into the current state of the offsite construction industry, exploring its growth, the impact of sustainability and innovation, the challenges faced, and the future trends that promise to shape this dynamic sector.
Growth and Adoption of Offsite Construction Methods Across Industries
The offsite construction sector has experienced remarkable growth, with a surge in adoption across various industries. This growth can be attributed to several factors, including the need for quicker project delivery, cost reduction, and improved quality control. Offsite construction methods, such as prefabrication and modular building, allow for components to be manufactured in a controlled environment and then transported to the construction site for assembly. This process significantly reduces the time spent on-site, minimizes labor costs, and enhances overall project efficiency.
Real estate developers are particularly drawn to offsite construction due to its ability to meet tight deadlines and budget constraints. The modular construction market is projected to reach $157 billion by 2023, reflecting a growing acceptance of these methods. Furthermore, industries such as healthcare, education, and hospitality have embraced offsite construction to meet increasing demands for space and rapid expansion.
In addition to traditional sectors, the offsite construction industry is also making inroads into the residential market. With the housing crisis affecting many regions, modular homes offer a solution that provides affordable housing options while maintaining quality and aesthetic appeal. As more developers recognize the benefits of offsite construction, the trend is likely to continue, paving the way for a more efficient and sustainable future in building.
Impact of Sustainability and Innovation on Prefabrication and Modularity
Sustainability has emerged as a key driver in the evolution of the offsite construction industry. As concerns about climate change and resource depletion grow, the need for environmentally friendly building practices has never been more pressing. Offsite construction methods inherently support sustainability by minimizing waste, reducing energy consumption, and promoting the use of renewable materials.
Prefabrication allows for precise manufacturing processes that generate less waste compared to traditional construction. The controlled environment of modular factories enables better resource management and recycling practices, which contribute to a lower carbon footprint. Additionally, the ability to incorporate sustainable materials and energy-efficient systems into prefabricated components enhances the overall sustainability of the final structure.
Innovation plays a crucial role in advancing offsite construction methods. The integration of advanced technologies, such as Building Information Modeling (BIM), robotics, and automation, has revolutionized the design and manufacturing processes. BIM allows for precise planning and visualization, reducing errors and streamlining collaboration among stakeholders. Robotics and automation enhance production efficiency, allowing for faster turnaround times and improved quality control.
As sustainability and innovation continue to intersect within the offsite construction industry, developers and contractors are presented with new opportunities to create buildings that are not only efficient but also environmentally responsible. This shift toward sustainable practices is expected to gain momentum, influencing design trends and construction methodologies in the years to come.
Challenges Faced in Regulatory Compliance and Logistics
Despite the numerous advantages of offsite construction, the industry is not without its challenges. One of the primary hurdles is regulatory compliance. Building codes and regulations can vary significantly from region to region, making it difficult for modular factory owners and developers to navigate the complex landscape. The lack of standardized regulations for offsite construction methods can lead to delays, increased costs, and complications in securing necessary permits.
Moreover, the logistics of transporting prefabricated components to construction sites pose another challenge. The size and weight of modular units can complicate transportation and delivery, particularly in urban areas with limited access. Coordinating the logistics of moving these components, especially when dealing with multiple suppliers and subcontractors, requires careful planning and management.
Additionally, there is a cultural resistance within the construction industry to fully embrace offsite methods. Many traditional contractors and stakeholders may be hesitant to adopt new technologies and processes, preferring to stick with established practices. Overcoming this resistance necessitates education and advocacy to demonstrate the benefits of offsite construction and build confidence in its effectiveness.
Future Trends and Opportunities Shaping the Industry
Looking ahead, several trends and opportunities are poised to shape the future of the offsite construction industry. The continued emphasis on sustainability will drive the development of eco-friendly materials and energy-efficient designs. As governments and organizations set stricter environmental regulations, the demand for sustainable building practices will only increase, positioning offsite construction as a leading solution.
Technological advancements will also play a pivotal role in the industry’s evolution. The rise of smart buildings and the Internet of Things (IoT) will lead to the integration of intelligent systems into prefabricated components. These innovations will enhance building performance, energy efficiency, and occupant comfort, creating a more appealing product for developers and end-users alike.
Furthermore, the ongoing labor shortage in the construction industry presents an opportunity for offsite construction to fill the gap. By leveraging automation and advanced manufacturing techniques, modular factories can produce high-quality components with fewer workers, addressing labor challenges while maintaining efficiency.
As the offsite construction industry continues to mature, collaboration among stakeholders will be essential. Real estate developers, modular factory owners, general contractors, and private equity firms must work together to share knowledge, resources, and best practices. This collaborative approach will foster innovation and drive the industry forward.
Conclusion
The offsite construction industry is at a pivotal moment, characterized by rapid growth, sustainability, and innovation. As real estate developers, modular factory owners, general contractors, and private equity firms navigate the challenges and opportunities within this evolving landscape, they must embrace new technologies and practices to remain competitive. By prioritizing sustainability and collaboration, the industry can continue to transform the way we build, creating efficient, high-quality structures that meet the demands of a changing world.
Key Takeaways:
- The offsite construction industry is growing rapidly, with a projected market value of $157 billion by 2023.
- Sustainability and innovation are driving the evolution of prefabrication and modularity, leading to reduced waste and energy consumption.
- Regulatory compliance and logistics remain significant challenges for the industry.
- Future trends include increased emphasis on sustainability, technological advancements, and collaboration among stakeholders.
As we move forward, the offsite construction industry holds immense potential to reshape the future of building, making it more efficient, sustainable, and responsive to the needs of society.